Boucler la boucle : la renaissance de l'unité Air grâce au recyclage
Innovation
Découvrez les coulisses de la fabrication circulaire des unités Nike Air.
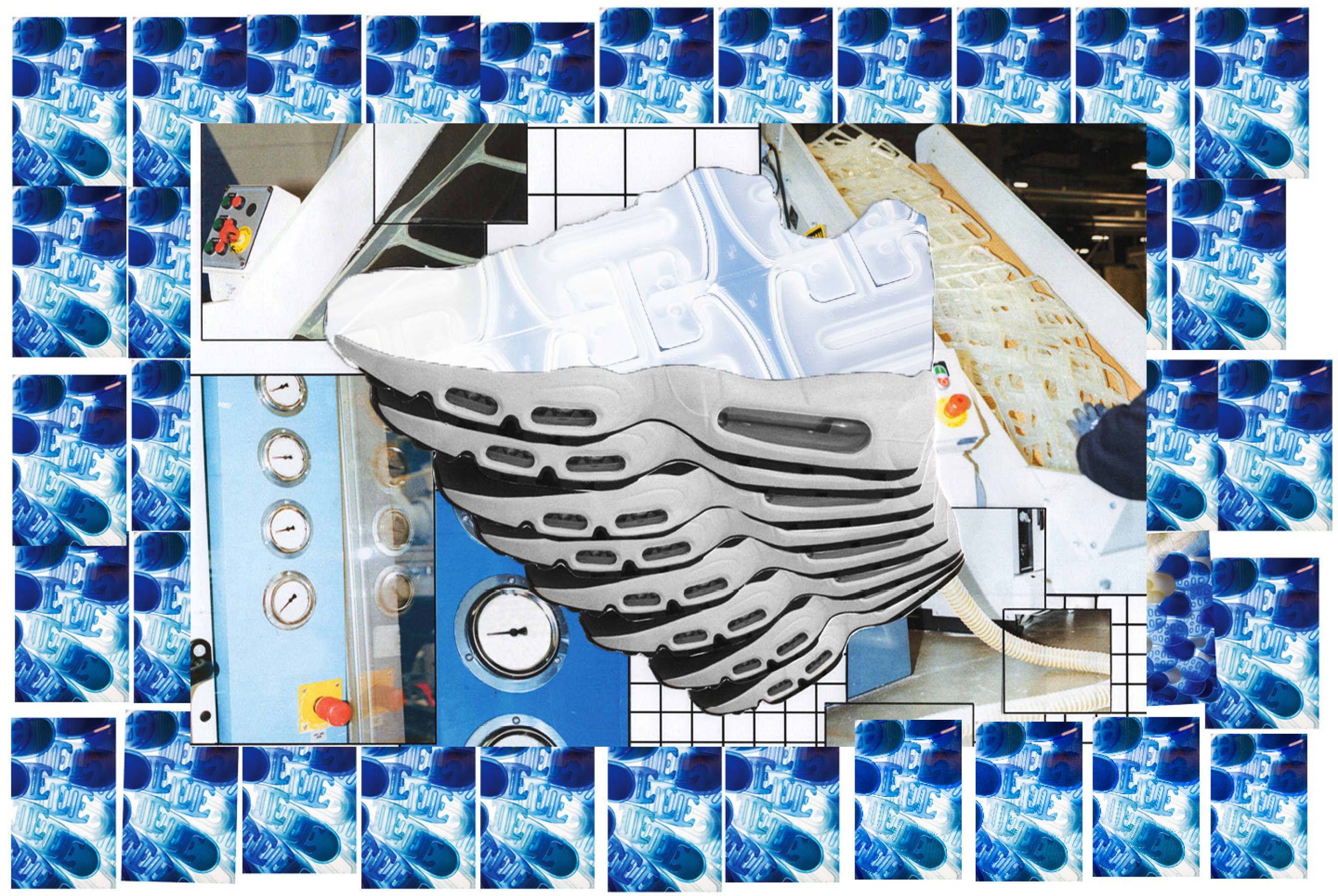
Présentée par Move to Zero : la démarche zéro déchet et empreinte carbone nulle de Nike pour protéger le futur du sport.
L'amorti Nike Air possède un riche héritage en termes de style et de confort, mais vous ne savez peut-être pas que son histoire légendaire comprend également des décennies d'innovation en faveur du développement durable. C'est vrai. Depuis sa création, Nike n'a cessé de faire évoluer cette technologie d'air sous pression afin de réduire son impact sur la planète.
« Depuis le début, nous avons sorti tellement d'innovations invisibles pour notre technologie la plus visible », explique Mitesh Patel, directeur des opérations de production du site Air Manufacturing Innovation (AirMI). « L'objectif est de garder une certaine cohérence, comme le look et les sensations, mais aussi d'améliorer continuellement la manière dont elle est fabriquée. »
Alors comment nous y prenons-nous ?
« Produire l'Air, c'est comme faire un gâteau, raconte Mitesh. Pour réaliser différents gâteaux, il faut des recettes différentes, et Nike a beaucoup de types d'Air différents. Chaque fois qu'un nouveau modèle est lancé, nous devons créer les machines et les processus nécessaires à sa réalisation. Nous utilisons les mêmes ingrédients, mais des méthodes différentes. »
Poursuivez votre lecture pour apprendre à préparer ce gâteau de l'espace. Pouvez-vous deviner comment nous ajoutons la production écoresponsable à la recette ?
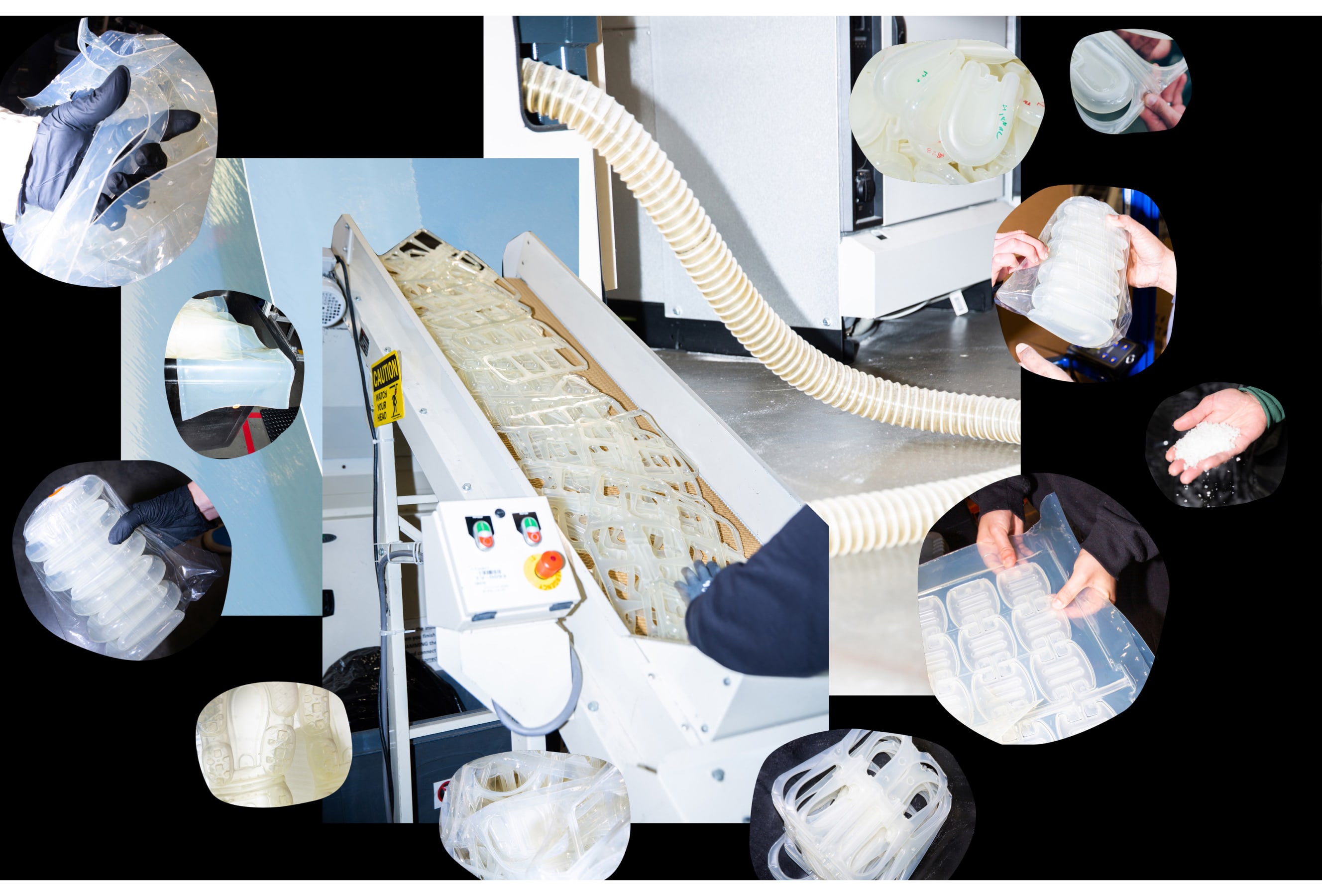
Les déchets issus du processus de production sont recyclés pour fabriquer de nouvelles unités Air. Ici, un aperçu du
processus exclusif photographié sur le site AirMI de Beaverton, dans l'Oregon, en janvier 2022.
Rassemblez vos ingrédients
De quoi est constitué l'amorti Air, au juste ? Il contient deux composants principaux, le premier étant le polyuréthane thermoplastique (TPU), un type de plastique apprécié pour sa robustesse et sa recyclabilité.
« Bien que le TPU ne soit pas recyclable à l'infini, nous sommes en mesure de le recycler encore et encore dans notre processus, explique Makely Lyon, responsable du programme de développement durable. Grâce à des décennies de pratique, nous avons affiné notre processus afin de recycler et de réutiliser une grande partie de ce qui serait autrement des déchets perdus. »
Ce TPU devient la paroi de l'unité Air, qui est ensuite remplie du deuxième ingrédient principal : le gaz. Cela peut paraître étrange, mais saviez-vous que l'air que nous respirons tous est un mélange de gaz ? Eh bien, la technologie Nike Air contient aussi du gaz. À l'origine, nous utilisions un gaz appelé hexafluorure de soufre (SF6) qui n'était pas très bon pour la planète.
This is a modal window.
« Notre équipe a compris la nécessité d'éliminer l'utilisation du SF6, un gaz au potentiel de réchauffement climatique très élevé, dès les années 1990, explique Makely Lyon. Il a fallu des années d'innovation. Mais depuis 2006, nous avons remplacé le SF6 par de l'azote à 100 %. »
Ce choix s'explique par la composition de l'atmosphère. En effet, l'atmosphère terrestre est composée d'azote gazeux à environ 78 %. C'est bien plus que l'oxygène, qui représente environ 21 % de l'atmosphère. Ainsi, si de l'azote s'échappe pendant le processus de fabrication, l'impact est moindre par rapport au gaz que nous avions choisi précédemment.
Vous avez votre gaz et votre plastique de folie ? Parfait. Maintenant…
Faisons de l'Air !
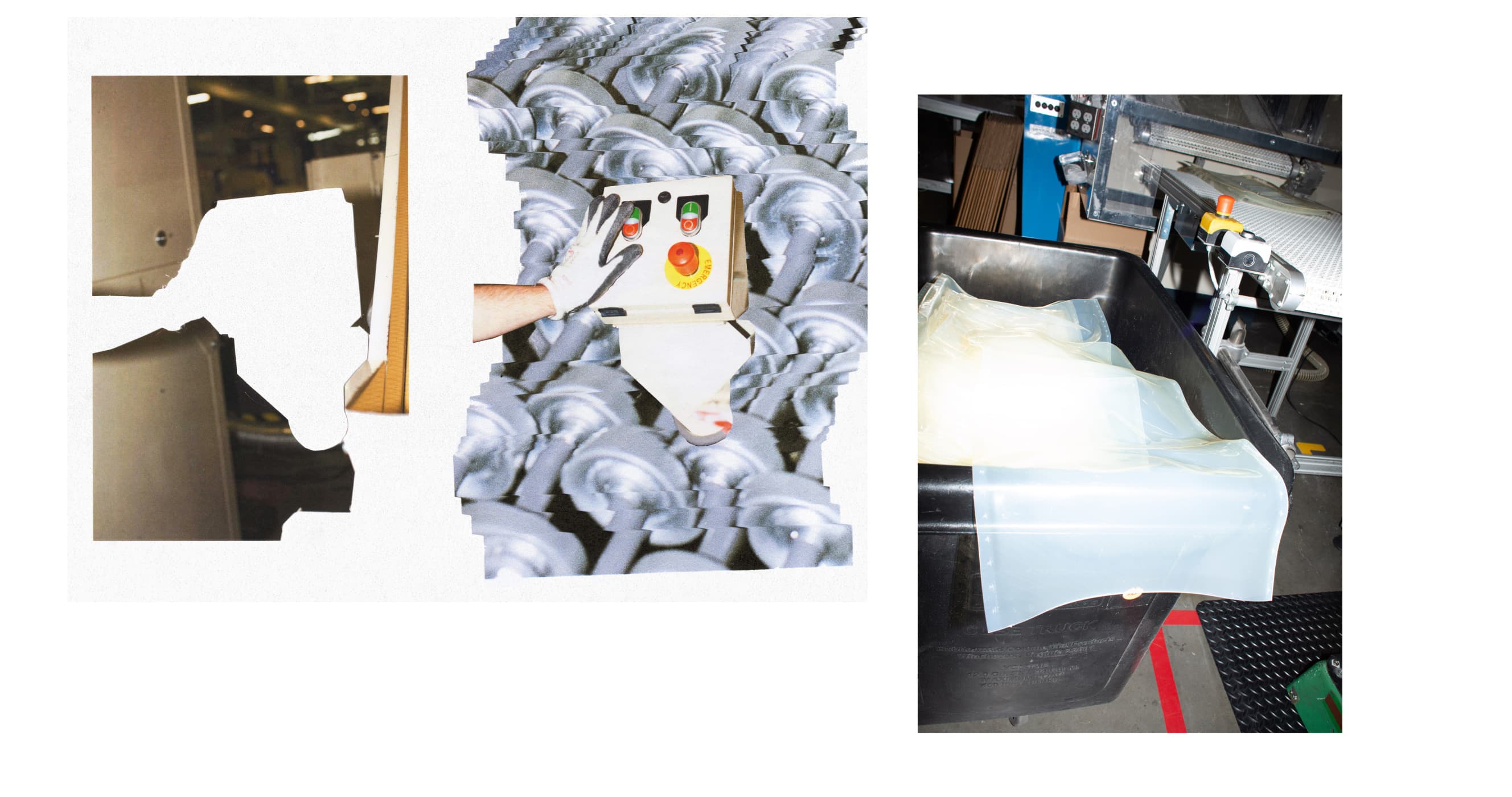
Étape 1 : Superposez deux feuilles de TPU, puis chauffez-les à la température idéale. La chaleur assouplit le TPU rigide pour que vous puissiez le mouler dans la forme souhaitée et le fermer, de manière hermétique, bien sûr.
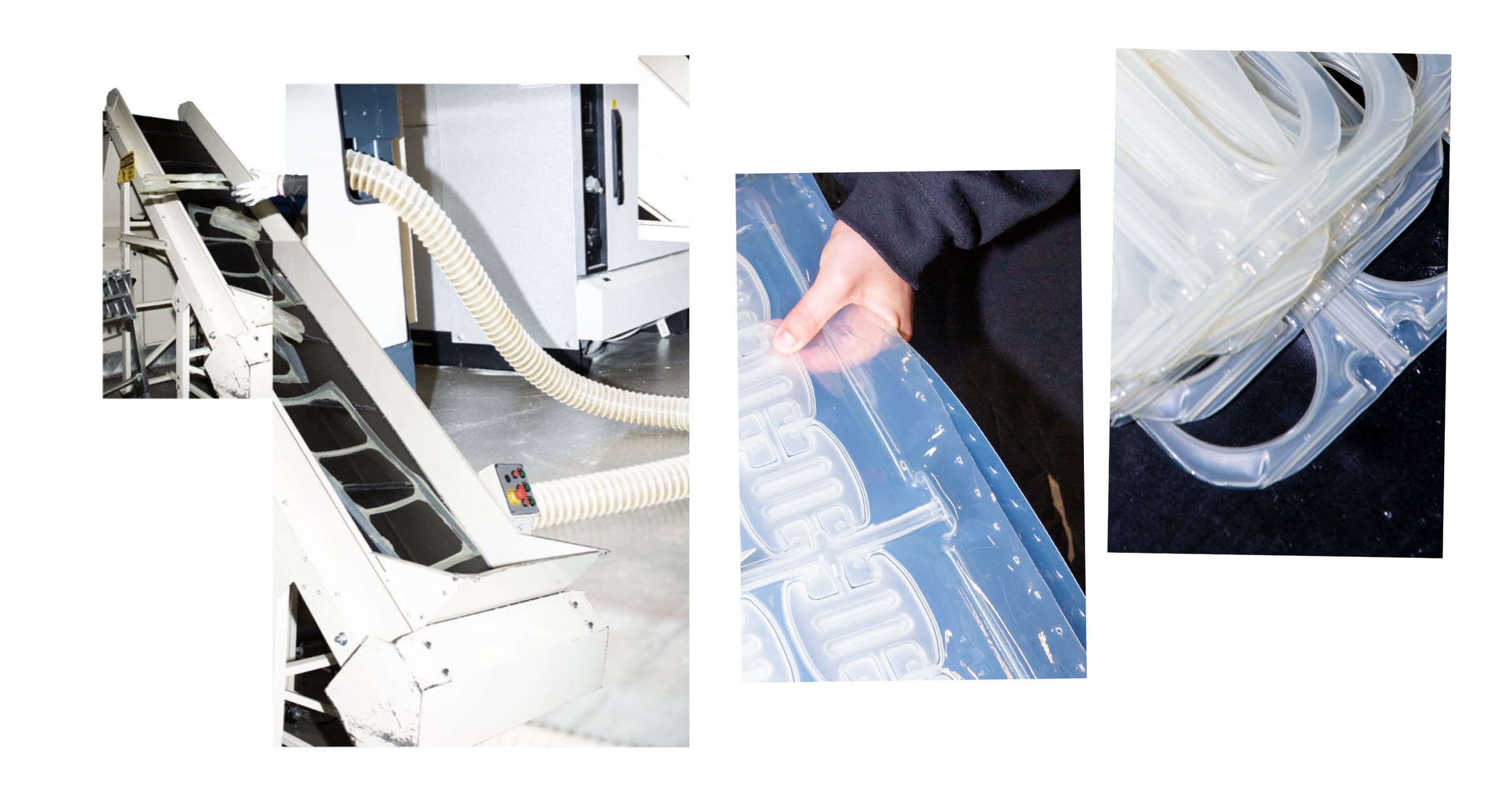
Étape 2 : Retirez les unités Air du moule une fois qu'elles ont pris, puis ôtez l'excédent de TPU pour affiner la forme. N'oubliez pas de conserver ces chutes ! Vous en aurez besoin pour la dernière étape.
This is a modal window.
Étape 3 : Injectez l'ingrédient pas si magique que ça : l'azote. C'est ce gaz qui remplit ces magnifiques coques en TPU pour donner le rebond que tout le monde connaît et apprécie.
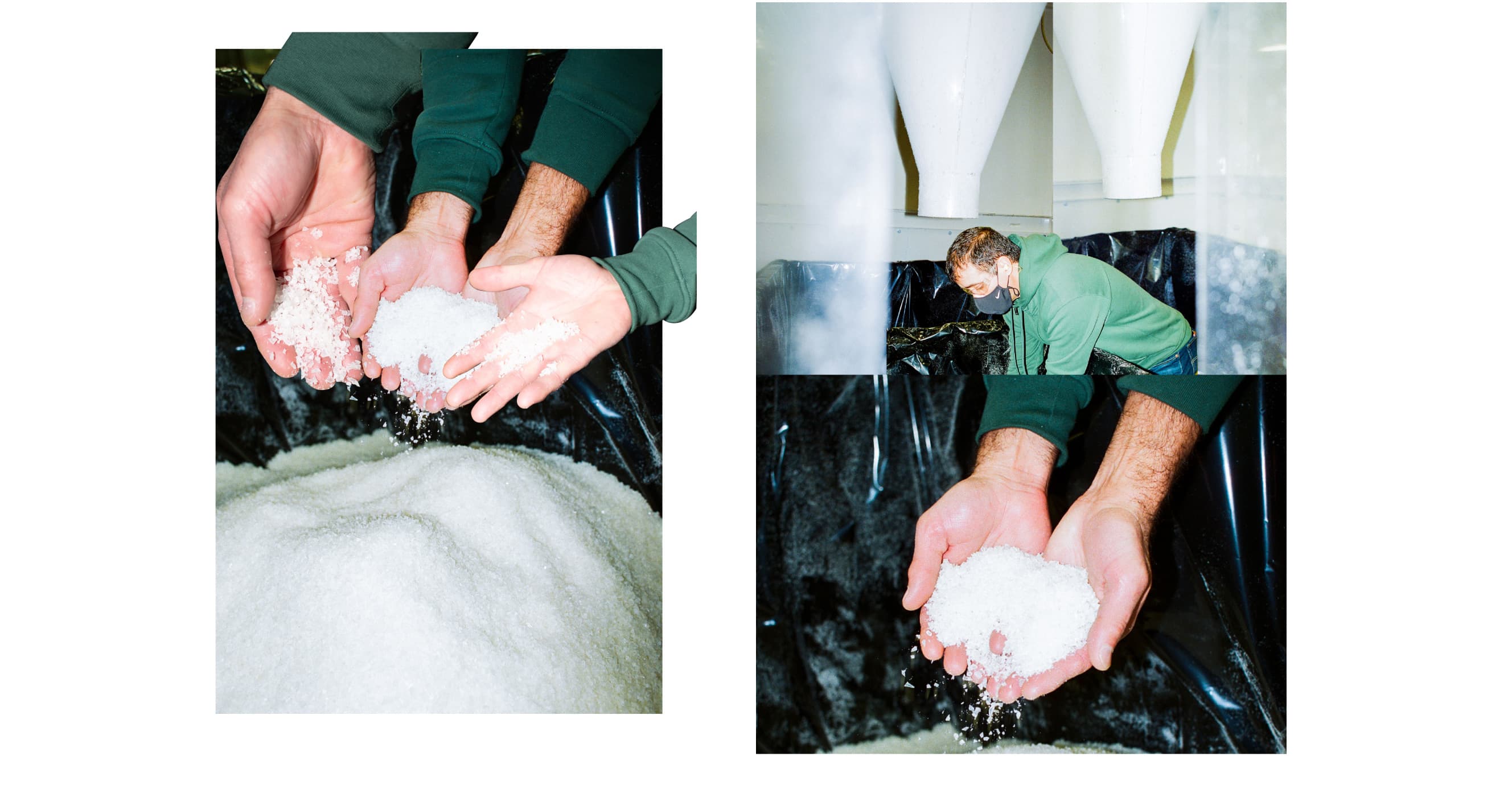
Étape 4 : Récupérez tous les déchets et chutes en bon état (soit plus de 90 % d'entre eux), puis broyez-les et faites-les fondre ensemble pour créer de nouvelles feuilles de TPU. Recommencez le processus. C'est le cercle de l'Air.
Et voilà, les unités Air sont prêtes à amortir vos pas et à ajouter une dose de matière recyclée à votre chaussure.
Avez-vous remarqué toutes ces modifications en faveur du développement durable ? L'utilisation d'azote au lieu de SF6 nous aide à réduire nos émissions de gaz à effet de serre. De plus, la réutilisation de tous les déchets de TPU nous a permis de détourner de la mise au rebut plus de 25 millions de kilos de déchets de production par an.
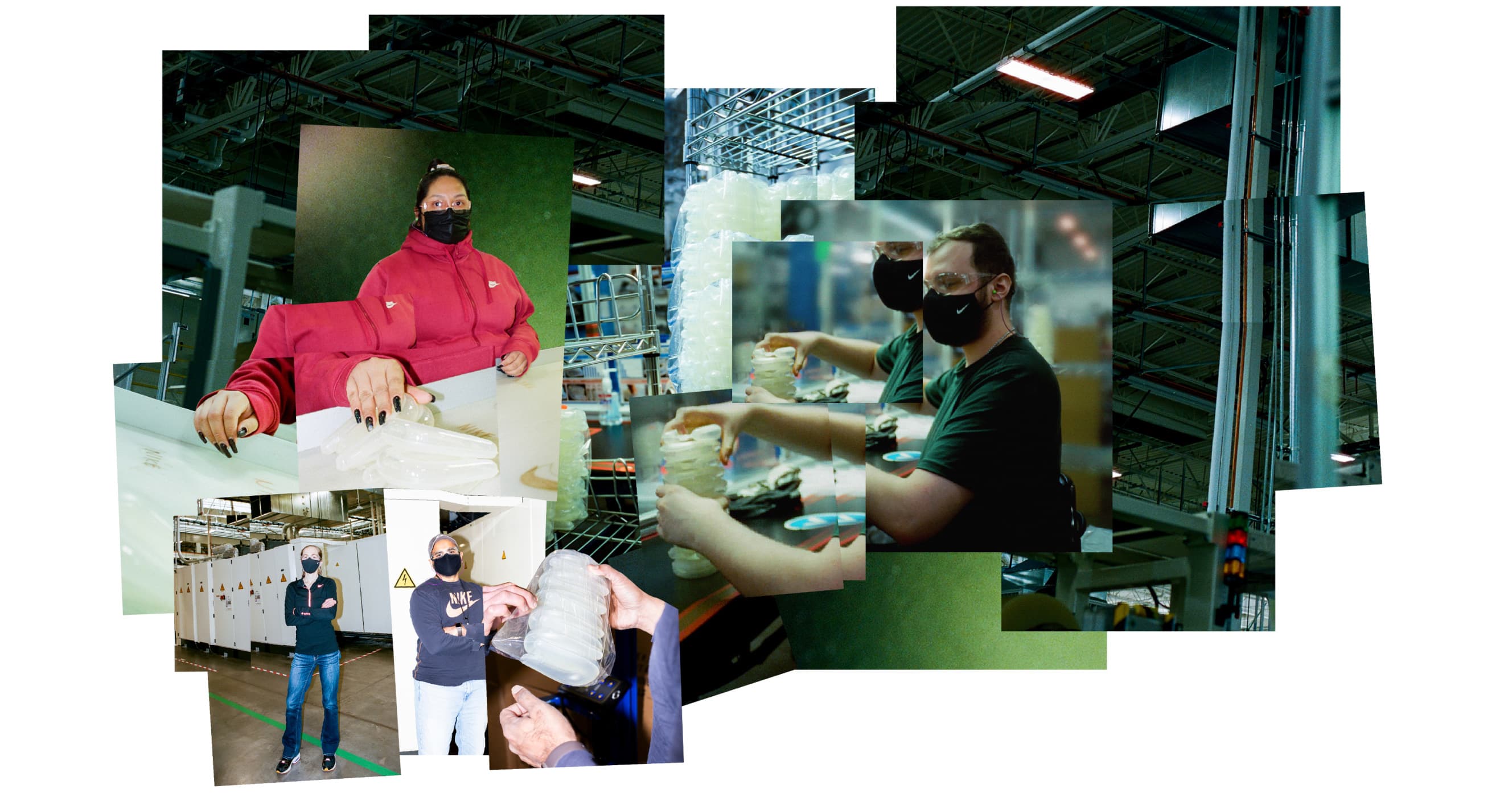
Membres de l'équipe AirMI, de gauche à droite : Makely Lyon, Ana Castaneda, Mitesh Patel et Jordan Binkerd.
Pour Makely, tout cela s'inscrit dans la « longue tradition d'innovation d'AirMI pour contribuer à réduire notre impact sur la planète. »
Compte tenu de ce passé, tout ceci n'est qu'un début.
« Nous faisons aujourd'hui des choses que l'on pensait presque impossibles il y a dix ans. C'est grâce aux gens. Sans eux et leurs idées, nous ne pourrions pas fabriquer la technologie Air. »
Mitesh Patel
Directeur des opérations de production du site Air Manufacturing Innovation (AirMI)
Pour plus d'informations : rendez-vous sur la page Nike.com/fr/developpement-durable pour suivre chaque étape de notre parcours et découvrir comment nous pouvons faire avancer ensemble la démarche Move to Zero.
Photographie : Ariel Fisher
Rédaction : Sallie Stacker