Full Circle: How Air Is Reborn With In-House Recycling
Innovation
Go behind the scenes to see how Nike Air units are made again, and again, and again.
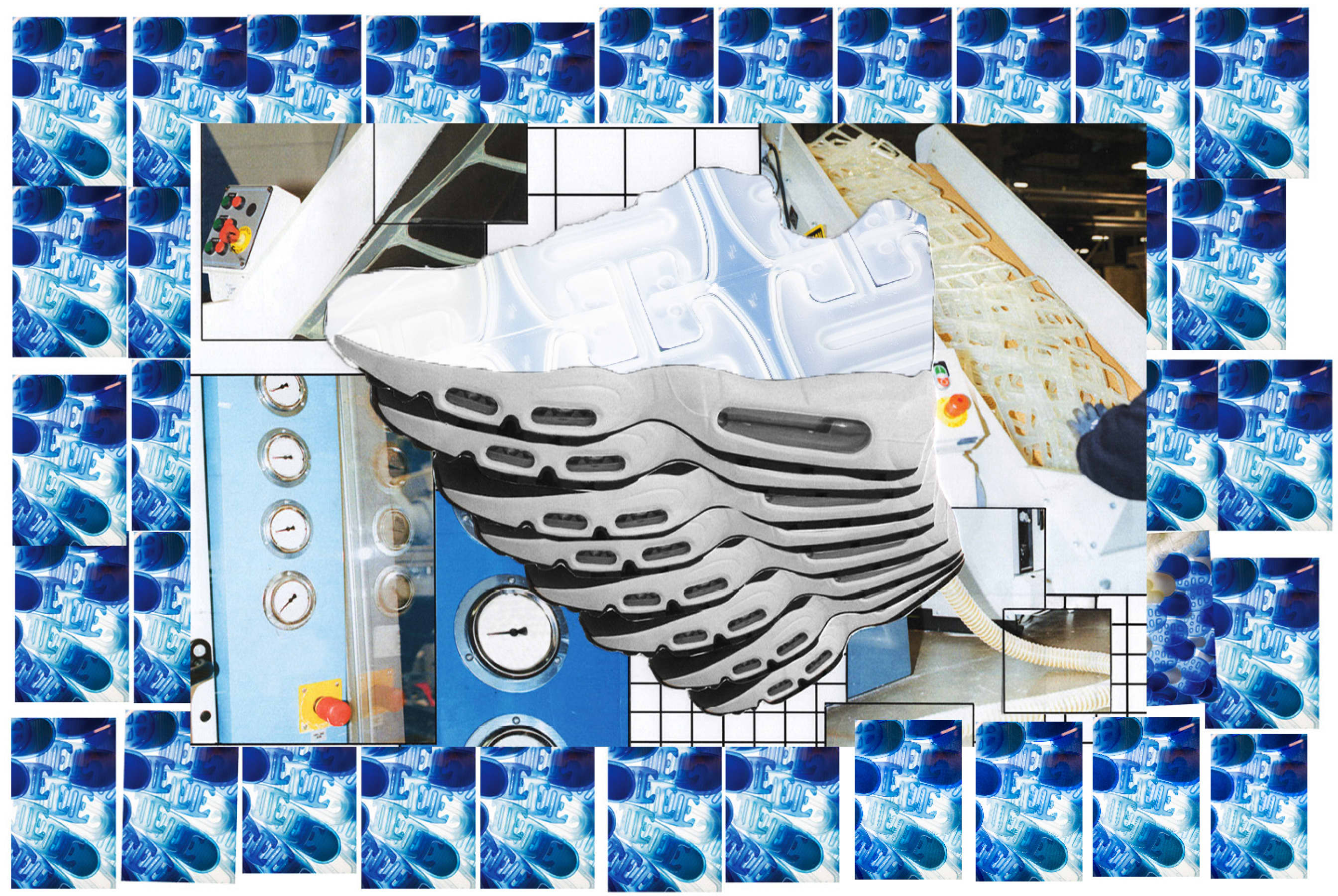
Presented by Move to Zero: Nike’s Journey toward zero carbon and zero waste to help protect the future of sport.
Nike Air cushioning has a rich legacy of style and comfort, but you may not know that its storied history also includes decades of sustainably minded innovation. It’s true. From its inception, Nike has constantly evolved this pressurized air technology to make less of an impact on the planet.
“Since the beginning we’ve launched so many invisible innovations to our most visible technology,” says Mitesh Patel, director of production operations at the Air Manufacturing Innovation (AirMI) facility. “The goal is to keep some things consistent — like the look and the ride — but to continually improve how it’s made.”
So How Do We Do It?
“Making Air is like baking a cake” says Mitesh. “Different cakes need different recipes, and Nike has a lot of different kinds of Air. Every time a new design comes in, we have to create the machines and processes to make it happen. It’s the same ingredients, just different methods.”
Follow along to learn how to bake this space-grade cake. Can you spot how we add responsible manufacturing to the mix?
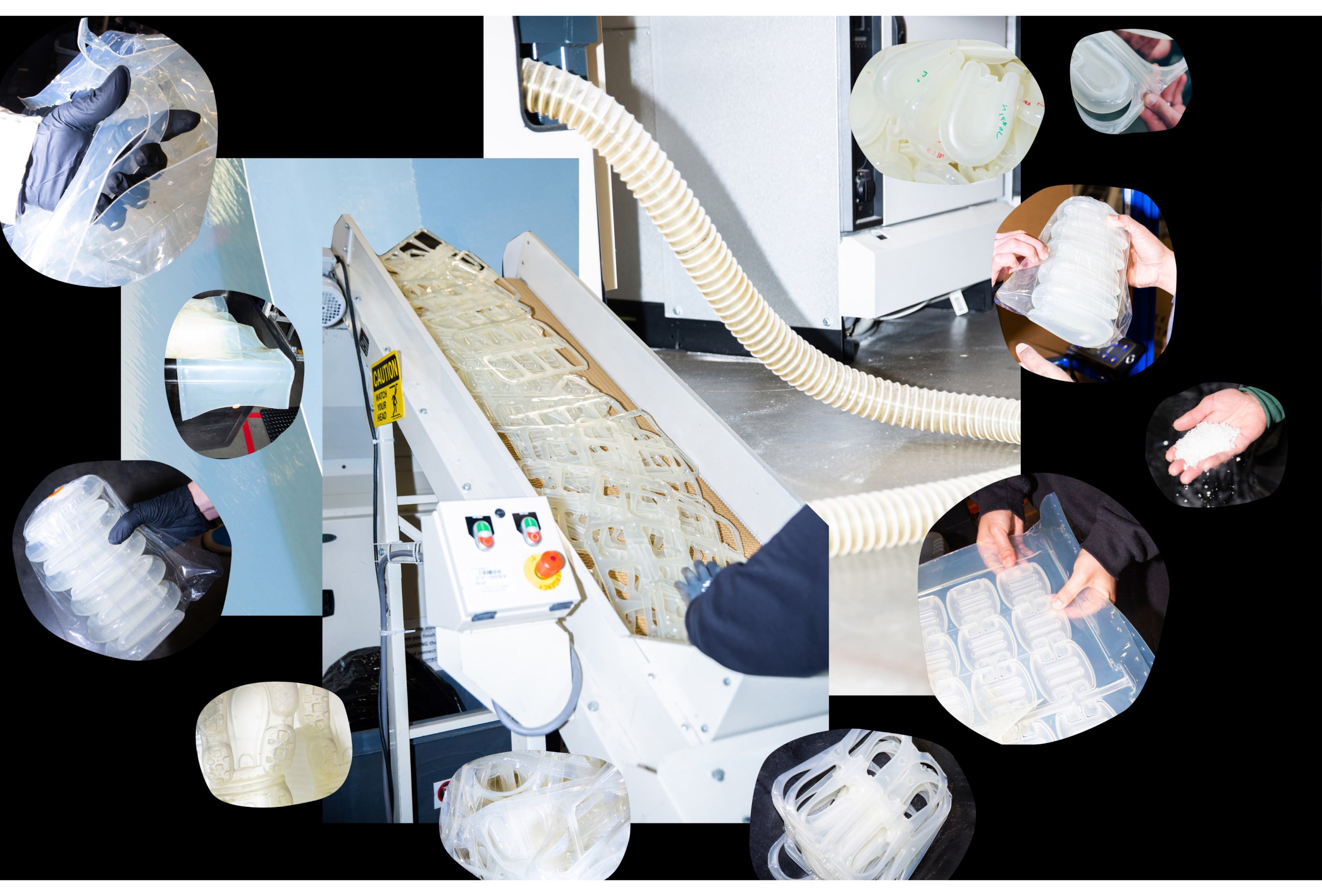
Scraps from the manufacturing process are recycled to make new Air units. Here, a glimpse of the
proprietary process is captured at the AirMI facility in Beaverton, Oregon in January 2022.
Gather Your Ingredients
What’s Air cushioning made of anyway? There are two main components, and the first is thermoplastic polyurethane (TPU), a type of plastic loved for its toughness and recyclability.
“While TPU isn’t infinitely recyclable, we are able to recycle it over and over again in our process,” says sustainability program manager, Makely Lyon. Thanks to decades of practice, we’ve refined our process to recycle and reuse much of what would otherwise be discarded scraps.
That TPU becomes the shell of the Air unit that’s then filled with the second main ingredient: gas. That may sound odd, but did you know that the air we all breathe is a mix of gases? Well, Nike Air contains gas too. Back in the day, we used a gas called sulfur hexafluoride (SF6) that wasn’t great for the planet.
This is a modal window.
“Our team recognized the need to eliminate the use of SF6, a gas with very high global warming potential, back in the ’90s” says Makely. “It took years of innovation. But since 2006, we have been SF6-free and use 100% nitrogen instead.”
That’s because approximately 78 percent of earth’s atmosphere is nitrogen gas, way more than oxygen which is roughly 21 percent. So if any nitrogen escapes during the manufacturing process, it has less impact than our previous choice in gas.
Got your gas and fancy plastic? Nice. Now…
Let's Make Some Air!
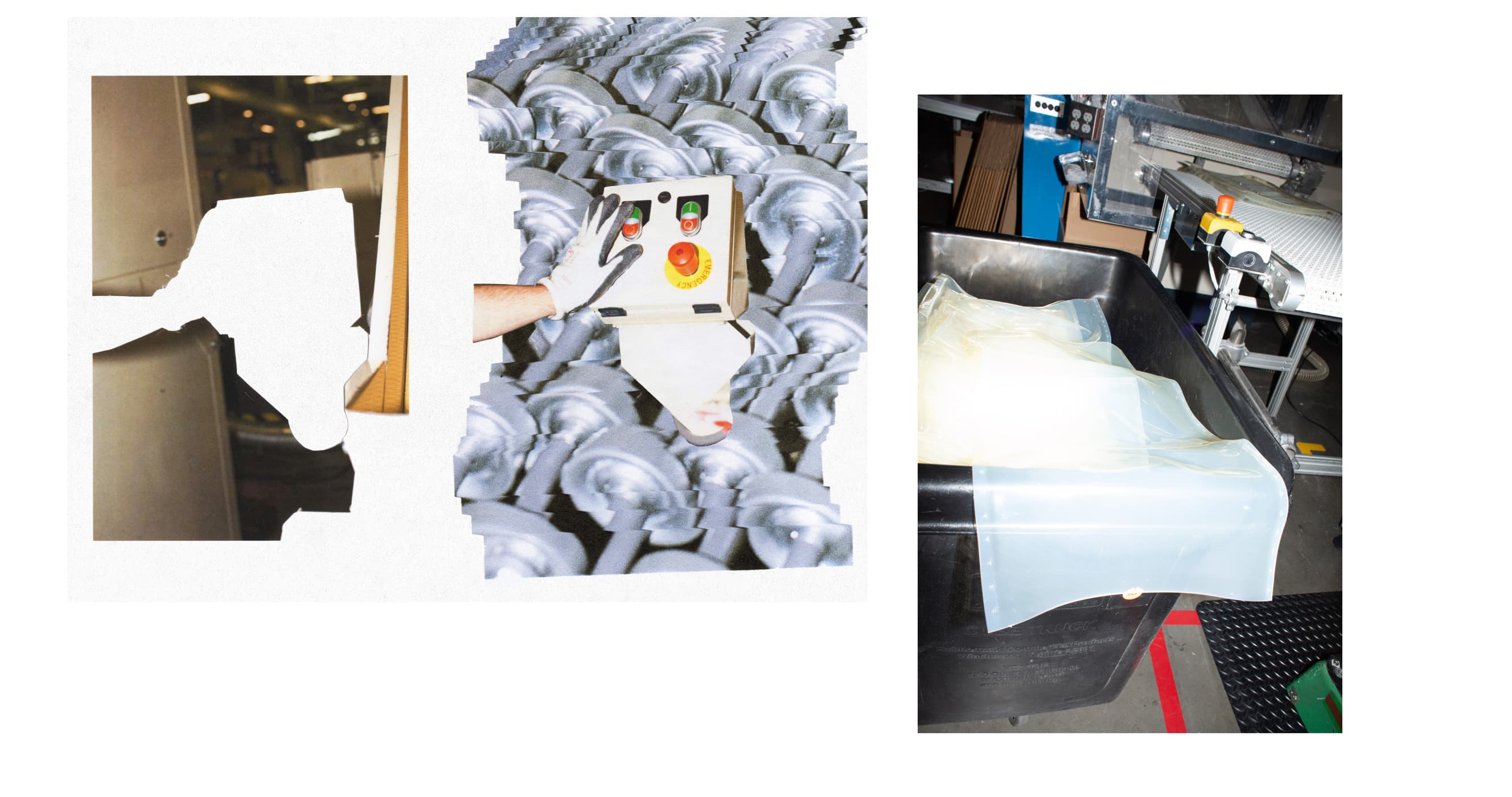
Step 1: Put two TPU sheets together and then heat them to the ideal temperature. All that heat makes the stiff TPU pliable so you can mold it into the right shape, and seal it — airtight, of course.
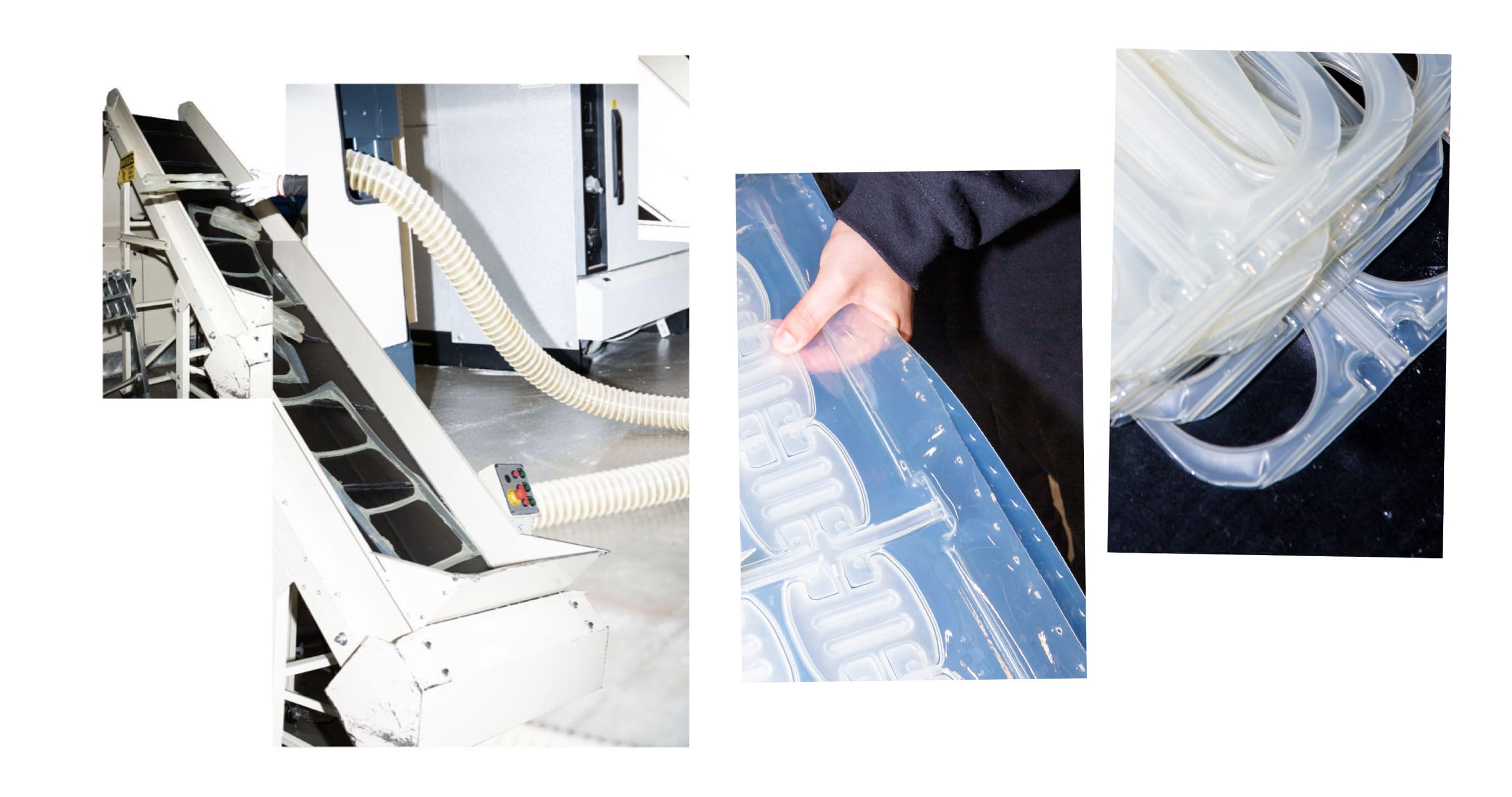
Step 2: Remove Air units from the mold once they’re set, then trim off any excess TPU to dial in the shape. Don’t forget to save those scraps! You’ll need them for the last step.
This is a modal window.
Step 3: Inject the not-so-magic ingredient — nitrogen. It’s what fills those beautiful TPU shells to give the bounce we all know and love.
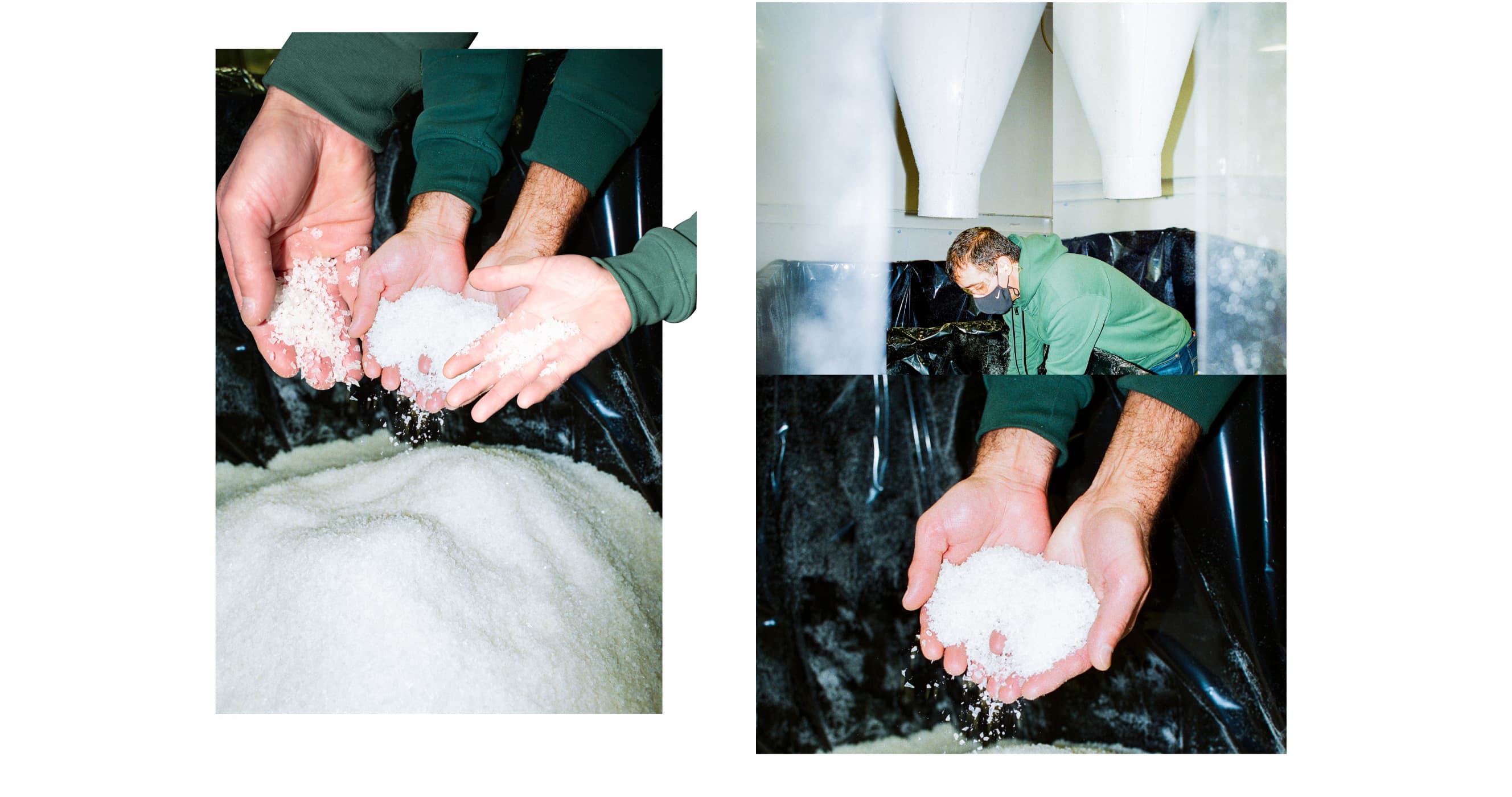
Step 4: Take all clean trimmings and scraps (which is more than 90 percent of ’em), then grind them up and melt them together to create new TPU sheets. Start the process again. It’s the circle of Air.
There you have it, Air units that are ready to cushion your step and add a dose of recycled material to your shoe.
Did you catch all those sustainably minded tweaks? Using nitrogen instead of SF6 helps us reduce our greenhouse gas emissions. Plus, reusing all those TPU scraps has helped us divert more than 60 million pounds of manufacturing waste away from landfills per year.
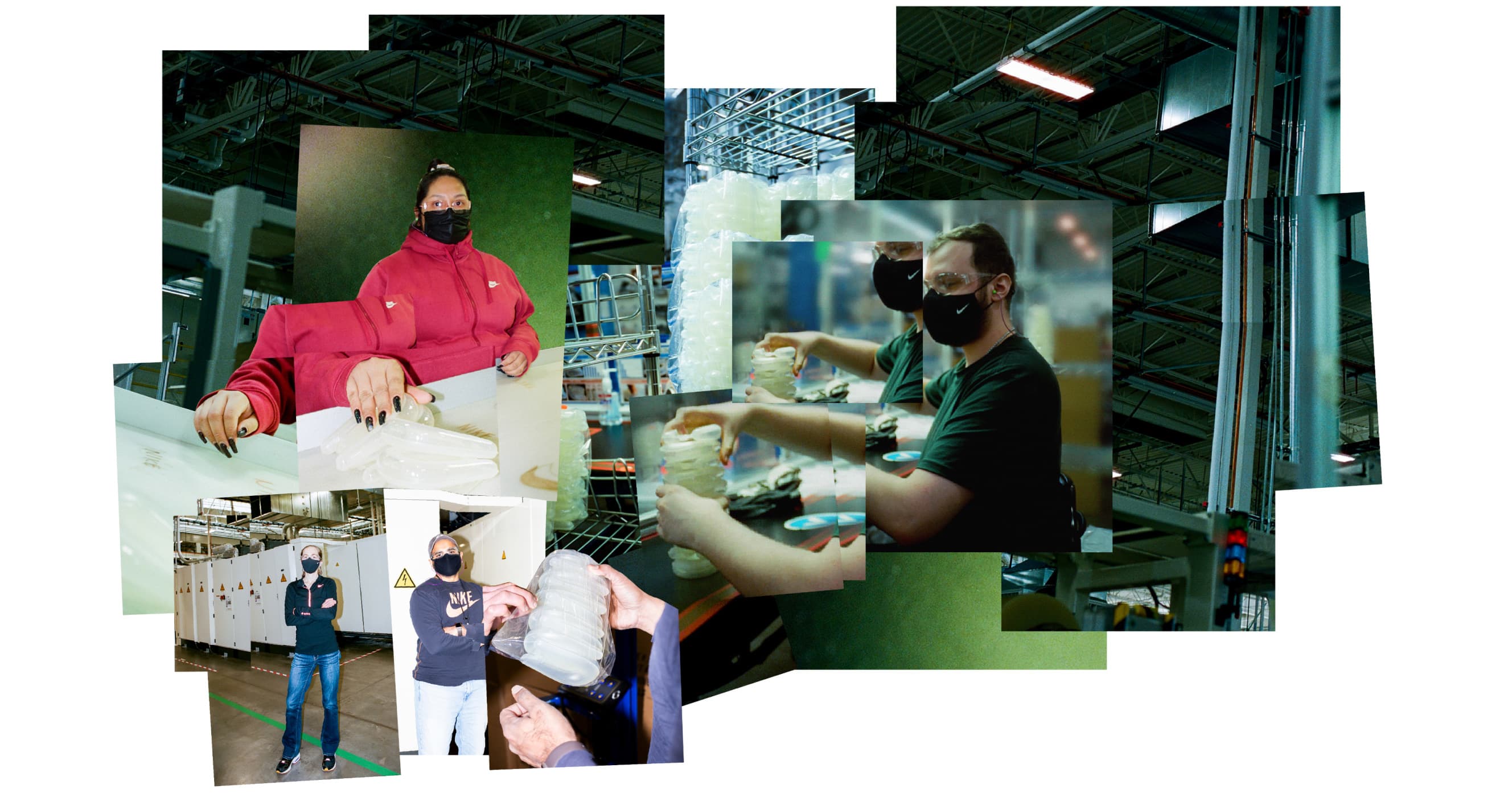
AirMI team members, from left to right: Makely Lyon, Ana Castaneda, Mitesh Patel and Jordan Binkerd.
According to Makely, it’s all a part of AirMI’s “long history of innovation to help reduce our impact on the planet.”
Given that history, this is just the beginning.
“We're doing things that were thought to be near-impossible a decade ago. That’s powered by people. Without them and their ideas, we can’t make Air.”
Mitesh Patel
Director of Production Operations at the Air Manufacturing Innovation (AirMI) Facility
For more: Visit Nike.com/Sustainability to follow each step in our journey and discover new ways we can Move to Zero together.
Photography: Ariel Fisher
Words: Sallie Stacker